How Coatings Can Cause Early Wheel Stud Failure
An often overlooked part of the puzzle are how coatings, in particular softer, thicker sprayed on coatings, used on components of the wheel joint have potential to cause detrimental effects on wheel stud life.
In general, spray coatings that apply thicker than 0.001" (0.03mm) should be avoided on surfaces that are subjected to clamp pressure in an important bolted joint (like keeping wheels on a race car). For example, paint/powder-coat often used on wheels can be in the range of 0.003"-0.006", and sometimes thicker depending on application variables and surface geometry (i.e.- wheel lug nut seats).
Often they can extrude away from the mating surfaces due to high clamp pressures from stud preload, assisted by elevated temperatures of the track environment. This scenario causes a large loss of stud preload; a precursor to stud failure.
As briefly discussed in our "Wheel Stud Torque & Friction" section, stud preload is the single most important parameter for studs/bolts to live a long life, assuming the joint is designed correctly (automotive OEM's figured this out).
In the case of the Zimmerman OE Z-coated rotor, the coating thickness is borderline, being anywhere from 0.008-0.001" thick (figures 1 and 2 show a brand new Zimmerman rotor after a one track day). So, you may be asking, "does this really matter then?"
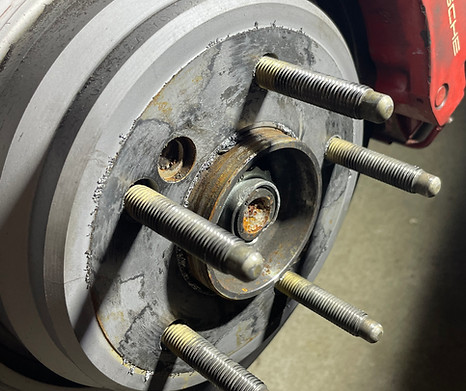
Figure 1: Zimmerman Rotor After Trqck Time

Answer: YES IT DOES! Especially if the car is track focused. Here's why:
When a bolted joint is initially tightened, there is a clamping force (preload) generated by the stretch of the bolts/studs, which behave as a very stiff spring, i.e.- they elongate a certain amount when preloaded: Force[F] = SpringRate[k] x ChangeInLength[x] (F=kx).
Conversely, the components in the wheel joint compress a certain amount as well, including whatever coatings may be on them. The "stiffness" of the clamped components play an integral part in the function of the wheel joint.
Figure 2: Close-up of a New OE Zimmerman Z-coated Rotor After Track Time

Figure 3: Cross section of Bolted Wheel Joint Components
Because bolts/studs are very stiff (spring rate), they only stretch a miniscule amount when preloaded; even at the incredible preload levels that they're capable of:
OEM strength (10.9) M12 wheel studs can be preloaded to 15,000 lbs repeatedly without any permanent stretching. Class 12.9+ M12 (Core4. MSI, & ARP studs) at least 17% higher than that.
The amount of stud stretch is directly correlated to preload and its working length, or what is referred to as "grip length" in the fastener engineering world (see Figure 3). The grip length of the stud is dictated by how thick the stack of components is in the joint.
The longer the grip length, the more they will stretch vs. the shorter grip length at the same preload.
Think about this like two suspension coil springs that are the same spring rate, but different lengths: the longer spring will compress more at the same force than the shorter one.
In this case, wheel studs in a typical wheel joint can stretch anywhere from 0.002" to 0.006" once preloaded (a piece of paper is ~0.004" thick). The relationship of stretch to preload is linear (F=kx).
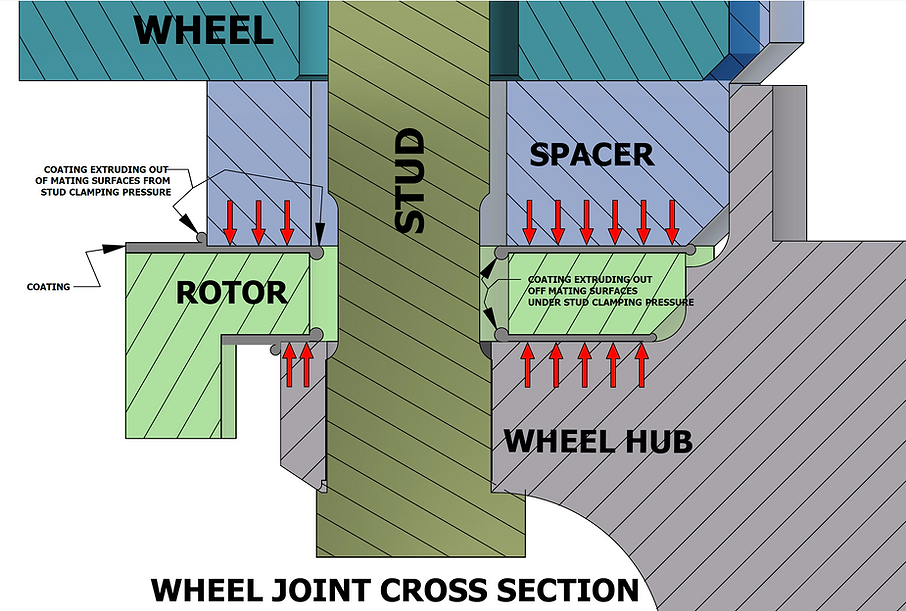
Figure 4: Visualization of Coating Extruding in Wheel Joint
So, if a rotor (or any joint component) has a coating that is 0.001" thick and can extrude out from the mating surfaces after the studs are fully tightened, there's potential for 0.002" (0.001" per side of rotor surfaces) of stud stretch to be lost to make up for the lost thickness of the coating extruding away (see Figure 4 for visualization).
An wheel stud losing 0.002" of stretch can equate to over 5000 lbs of LOST PRELOAD, which reduces the friction grip of the clamped components significantly.
This can lead to further lug nut loosening allowing wheel joint components to lose friction grip (slip relative to one another), which can lead cause crack formation in the studs, then potential wheel loss (figure 5).
This can be amplified due to the high variance of stud preload with the torque tightening method when using standard lug nuts. Our FLug nuts reduce this variance substantially by ensuring sufficient and consistent preload at a given tightening torque.
In the case of Zimmerman rotors, this effect will be worst when they are brand new during the first few track sessions. This is why we highly recommend to just remove the coating on both sides of the rotor when they are new with a wire brush wheel or similar to remove any variable that facilitates any loss of preload.
Now, keep in mind that paint and powdercoating that is used for finishing wheels is in the 0.003"-0.006" thickness range. That's 4 to 7 times thicker than the coating on Zimmerman rotors. This is why the wheel mating surface and lug nut seats are always raw aluminum finishes on any reputable wheel.
If you want to get your wheels painted, make sure these areas are always masked off!
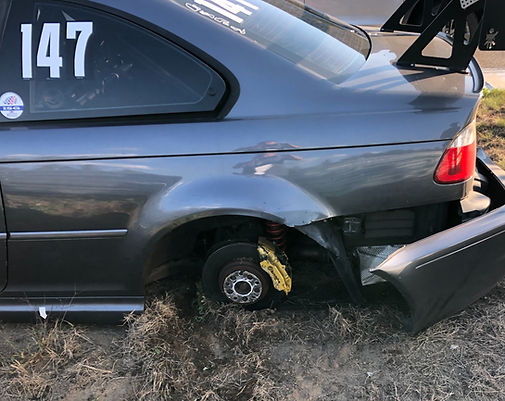
Figure 5: Wheel Loss Example due to Stud Failure